SELECTIVE LASER SINTERING
Selective laser sintering is an additive manufacturing technique that uses a laser as the power and heat source to sinter powdered material, aiming the laser automatically at points in space defined by a 3D model, binding the material together to create a solid structure.
Advantages of SLS Technology
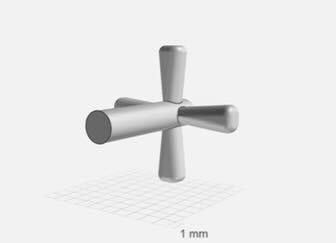
No need for supports
SLS 3D printing does not require supports, due to the uncured powder acting as a natural support. This makes it possible to print complex structures without having to remove additional components after the process.
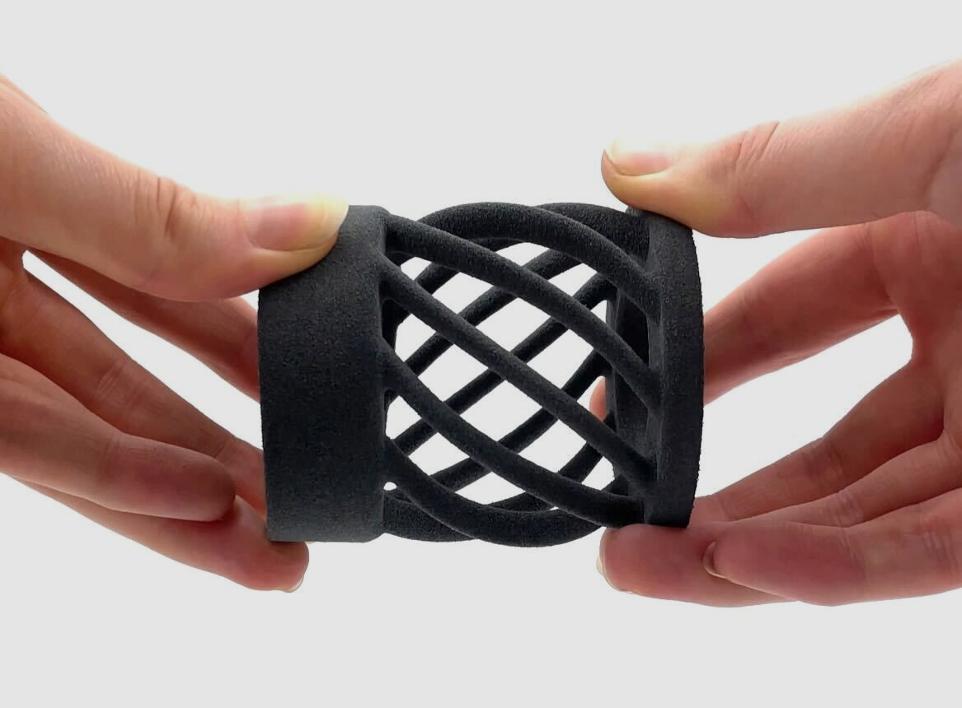
High precision
SLS technology produces precise and accurate details in printed objects, making it suitable for advanced prototypes and final products.
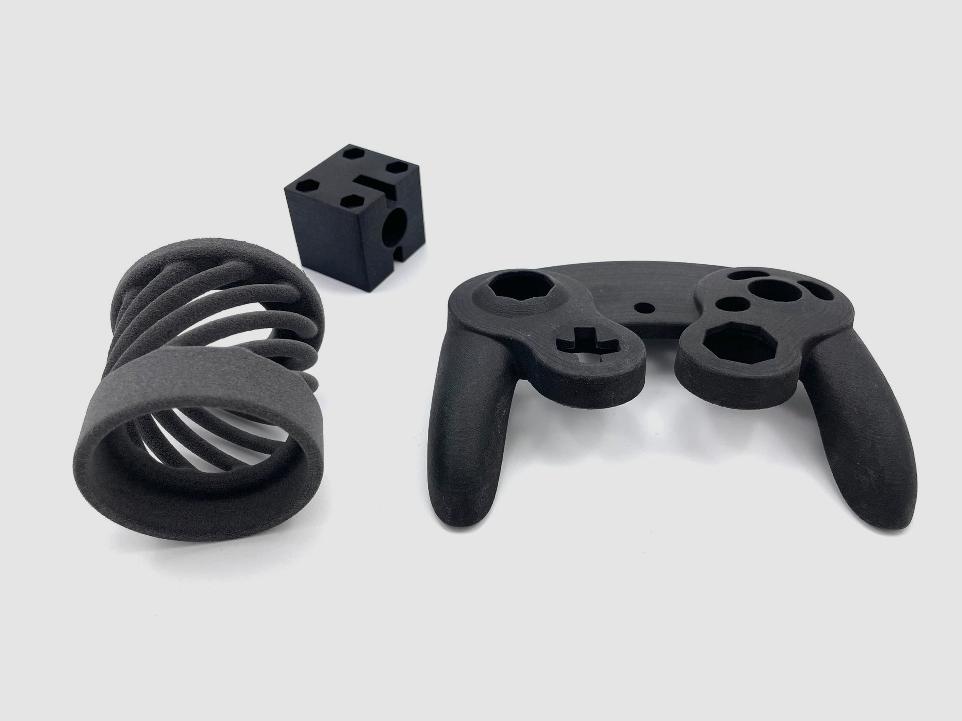
Wide variety of materials
SLS is not limited to just one type of material. Powders used in the process can include polymers, metal, ceramics, etc. This makes the technology versatile and adaptable to different applications.
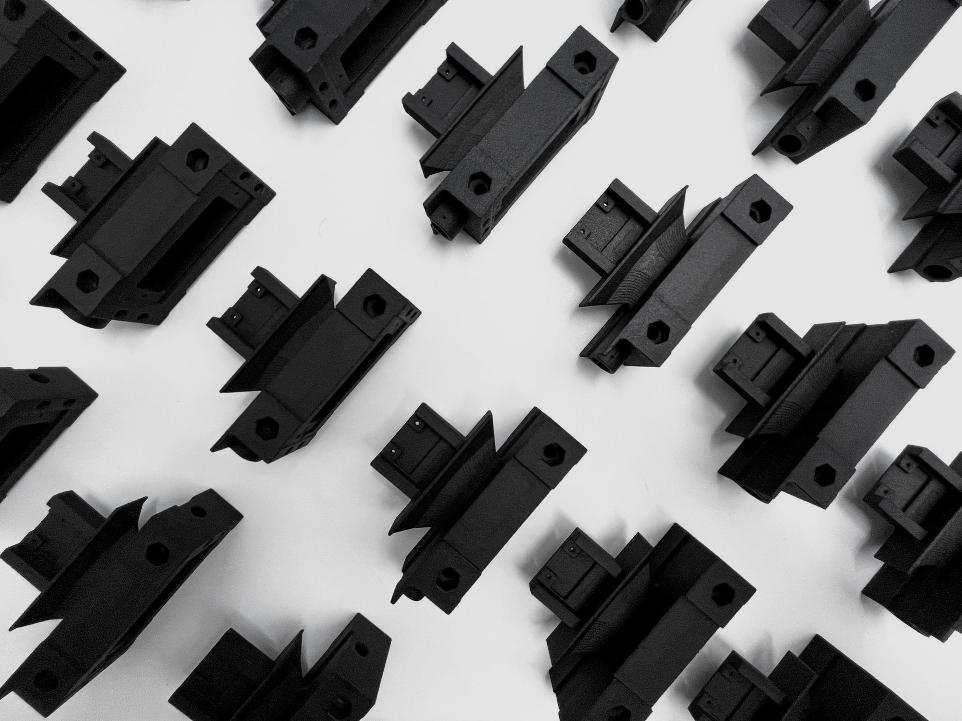
Producing more parts at once
With SLS technology, multiple objects can be printed at the same time, speeding up the process and making it more economical, especially for small-scale production.
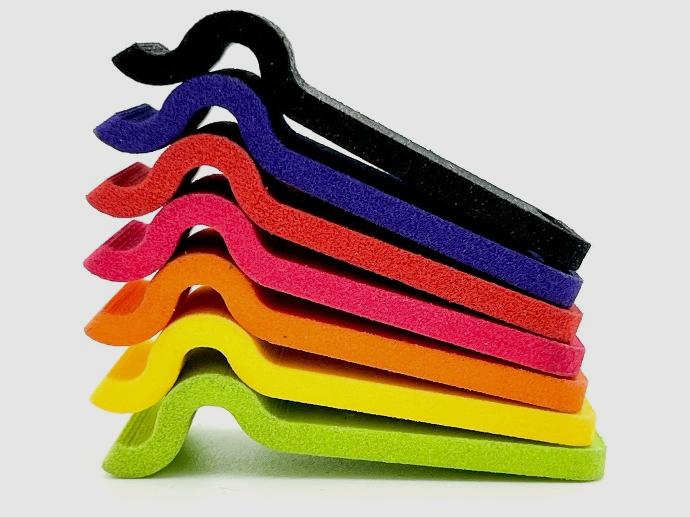
Availability of different colours
In our company there is a choice of deying the print in different colours such as black, blue, red or yellow. We also have a variant of polyamide 12 in natural black, which owes its colour to the added pigment.
Fast production
Functional parts on your desk in 5 days.
Automated post-processing
Finished parts right out of the 3D SLS printer.
Industrial scale
We can deliver 1,000 parts to you in a month.
Repeatability
Production to the highest standards.
Stages of 3D printing in SLS Technology
STAGE 1 "DATA PREPARATION"
The process starts with the preparation of the cell design. At this point, the operator decides in which orientation the parts will be printed. Unlike other 3D printing techniques in the case of powder, we can place the parts one above the other or even one inside the other.
STAGE 2 "PREPARING THE 3D PRINTER"
We prepare the printer for printing by loading the chamber design and filling the feed container with the correct amount of powder.
STAGE 3 "PREHEAT"
Once the carriage is placed in the printer, preheating of the chamber and the printer work area begins, keeping the temperature below the melting point of the polymer used for printing.
STAGE 4 "PRINT"
In the laser printing process, a focused laser beam, operating in infrared, scans the print layer representing a cross-section of the chamber design heating the powder to its melting point at this point. Once the layer is finished sintering, the working chamber moves down and the squeegee applies a new layer of powder. This cycle repeats, with each layer being scanned and sintered, resulting in a layered 3D print.
STAGE 5 "UNPACKING"
After printing, the 3D print cools down. First slowly in a controlled manner to avoid thermal deformation and then naturally until the temperature reaches less than 50°C. At this point, the operator can unpack the chamber and separate the parts from the uncooked powder using compressed air with a slightly abrasive medium.
STAGE 5 "UNPACKING"
After printing, the 3D print cools down. First slowly in a controlled manner to avoid thermal deformation and then naturally until the temperature reaches less than 50°C. At this point, the operator can unpack the chamber and separate the parts from the uncooked powder using compressed air with a slightly abrasive medium.
Why choose 3D printing?
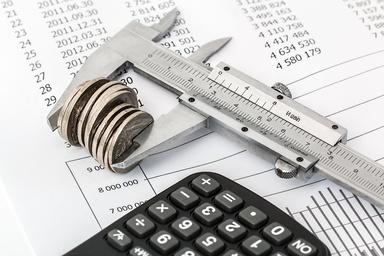
Non-capital expenditure
3D printing allows for the creation of parts without the use of expensive injection molds or machining tools. This process can be more cost-effective for small quantities because the cost of producing the parts does not depend on the number of units produced.
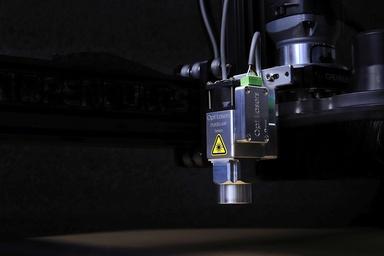
Zero Lead Time
Additive Manufacturing can be very fast, allowing for the rapid creation of parts in low quantities. Compared to traditional manufacturing methods such as extrusion, injection molding, or milling, 3D printing allows for much shorter production times.
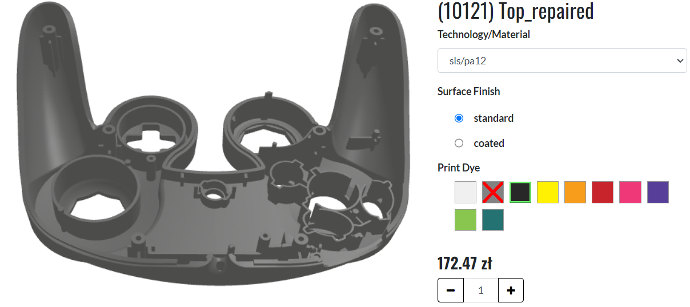
Customization
3D printing enables the creation of parts that are customized to individual customer needs. Instead of mass production, unique parts can be created for each customer with specific specifications
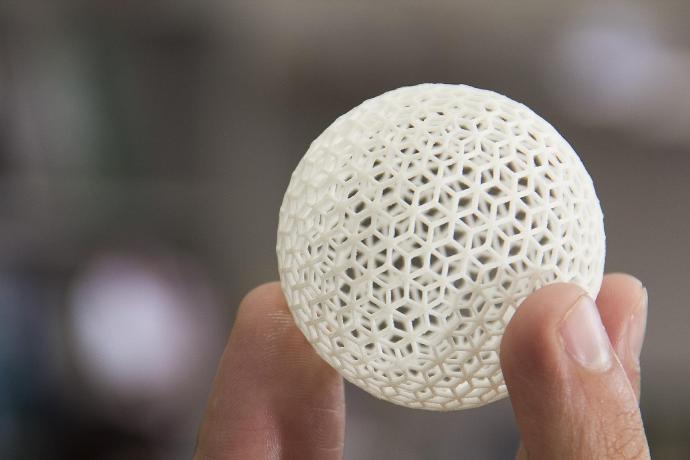
Flexibility
3D printing allows for the creation of parts from different materials, including plastics, metals, ceramics, and others. This process can be used to produce a wide range of parts, depending on customer needs.